Ultrasonic Plastic Welding Machines Florida seals parts together in a very short timeframe. The food industry uses this technique to seal products such as milk and juice containers.
The process involves a generator converting electricity into high-frequency ultrasonic energy, a converter turning that energy into mechanical vibration, and a booster amplifying those low-amplitude vibrations. A controller manages the welding process.
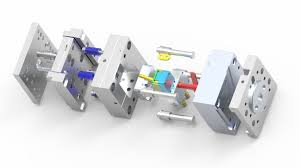
Ultrasonic Plastic Welding Machines are an efficient alternative to manual welding processes. The ultrasonic vibrations create strong, durable bonds between plastic components without adding extra materials or time to the process. Additionally, the welds are clean and strong enough to hold the assembled parts together without the need for bolts or nails. This makes the ultrasonic welding process ideal for a wide range of industries.
The weldability of plastics depends on the material’s structure and melting point, or Tg. Softer, amorphous materials such as polyphenylene oxide and acrylonitrile butadiene styrene are the easiest to weld with an ultrasonic machine, while more hard and rigid materials like acetal and polyvinyl chloride require a higher Tg for proper welding. The weldability of dissimilar plastics also varies based on their chemical compatibility and melt flow index.
The frequency of an ultrasonic welding machine affects the amount of energy applied to the welded materials, which in turn affects the quality of the weld. Higher frequencies produce more power than lower ones, making them suitable for welding thicker or larger-sized plastic parts. Choosing the right frequency for a particular project requires testing with samples of each type of plastic to determine the optimal setting.
Once the welding frequency is determined, the welding sonotrode and horn of an ultrasonic plastic welder are adjusted to match the geometry of the welded part. The welding sonotrode converts acoustic energy into mechanical vibrations and transmits these vibrations to the weld interface, where they generate heat and cause plastic molecules to fuse together. The horn then applies pressure to the welds to keep them in place while the welds cool and solidify.
Like any other piece of equipment, ultrasonic welding machines must undergo regular maintenance to ensure they continue performing at peak efficiency. A common cause of poor weld quality is a worn sonotrode, horn or stack component. To prevent this, manufacturers should regularly check the welder’s washers, stack components and horn surfaces for wear using factory-recommended procedures. In the event of a worn component, the manufacturer should recondition or replace it to avoid a decrease in performance and weld quality.
Sustainability
Ultrasonic plastic welding machines use high-frequency electrical energy to generate mechanical vibrations that initiate plastic melt at the interface of two joined parts. The weld is made without changing the thermoplastic material’s state from solid to liquid, resulting in strong and seamless bonds that don’t require extra work steps or aids such as glues or solvents. This means that welds are cleaner and more environmentally friendly than other methods, aligning with modern sustainable manufacturing practices.
Unlike many other industrial processes, ultrasonic plastic welding requires significantly less energy, making it an energy efficient technology. Additionally, it eliminates the need for chemical adhesives or solvents that typically release harmful emissions during production. Using an ultrasonic welder reduces production time and waste while improving worker safety.
The key to successful ultrasonic plastic welding is a good understanding of a plastic’s melting behavior and its ability to bond with dissimilar materials. This is based on the material’s “glass transition temperature” or Tg, as well as its chemical compatibility and Melt Flow Index (MFI), which quantifies how easily a plastic will convert to a liquid state.
With the right converter, booster, and weld horn, an ultrasonic welder will be able to accurately deliver the amplitude needed for a specific thermoplastic’s Tg and MFI. Trial and error is often required to determine the optimal amplitude for a new application, but most suppliers of ultrasonic welders will have a wide range of amplitude data available to help you get started.
An ultrasonic plastic welding machine is an efficient, economical, and versatile method for joining and reforming thermoplastics in a variety of industries. It’s also an ideal option for creating hermetic seals on items such as cigarette packaging, where the plastic must be airtight to protect its contents from heat, chemicals and vapors. In addition, it can be used to create strong, durable connections in aerospace applications that rely on lightweight yet robust components. In fact, it is often the only possible way to assemble aircraft parts that need to be extremely lightweight, as they cannot be subjected to the high temperatures associated with traditional welding techniques.
Material Versatility
The mechanical vibration of ultrasonic welding creates heat by melting the interface between two plastic parts. The resulting welds are strong and durable, resistant to tension, shear and peel forces. These welds are also clean, contamination-free and mark-free.
Ultrasonic welding can be used with a variety of thermoplastic materials, including dissimilar plastics. This versatility means it is a great alternative to traditional welding methods, which typically require extensive sanding and buffing of the weld joint. Ultrasonic plastic welding is a process that can be used with a wide range of shapes and sizes, making it an ideal option for applications with tight space constraints.
With the right setup, ultrasonic welding can also be used to weld different materials together. The key to this is the amplitude, which refers to how much mechanical vibration the welding stack generates. For most applications, the converter (sonotrode), booster and weld horn must be carefully designed to deliver an amplitude that will efficiently initiate melt at the interface between two plastic components. Amplitudes that are out of range can result in poor bonds or even destruction of the materials altogether.
This is why advances in generator technology and power modules are critical. By regulating line voltage, these technologies ensure that the converter and booster operate within tightly controlled amplitude parameters. The weld horn is the pathway for these vibrations to the materials to be welded. A well-designed energy director focuses the amplitude into the welding area, while also helping to align and focus the weld.
When designing an ultrasonic welding system, consider the plastic’s Tg, chemical compatibility and melt flow index (MFI). Tg is the temperature at which a solid forms into a liquid. A low Tg makes it easy for ultrasonic welding to join plastics. A high Tg, on the other hand, may make it difficult to weld the material.
Ultrasonic plastic welding is a valuable technique for manufacturing many different types of products. From rugged parts for agricultural machinery assembly to airtight packaging for explosives and fireworks, this method of joining plastics offers a reliable and robust solution. The welds produced are as strong as the base material itself, and can withstand the harsh environments that these items often endure — including extreme cold, dust, mud and water.
Safety
Unlike other welding methods that use electricity to create heat, ultrasonic plastic welding machines produce their heat by way of mechanical vibrations (ultrasound waves). These waves stimulate the molecular chains of the two materials to be joined, causing frictional heat and melting. Combined with the clamping force of the machine, this process allows two parts to be joined precisely.
This process works best for thermoplastic materials with an amorphous structure. This means that they melt gradually over a range of temperatures, which makes them easier to weld. The glass transition temperature, or Tg, of a plastic is an important factor in gauging its weldability. It is also necessary to consider chemical compatibility and melt flow index (MFI), as dissimilar plastics may be more difficult to join.
Aside from the initial power supply, which is connected to a sonotrode or horn and an electronic ultrasonic generator, ultrasonic welding equipment requires little maintenance and has few moving parts. This is a big advantage over other welding methods, which can be complicated to operate and require a lot of safety precautions.
Because of the low risk involved with using an ultrasonic welder, it can be used in more sensitive applications. For example, items like hospital gowns and sterile garments can be welded together using this method. This helps to reduce contamination and prevent the spread of disease, as well as providing a more hygienic working environment.
When using an ultrasonic welder, proper training is essential. This should include an understanding of the technology, safety protocols and emergency procedures. It is important that all operators understand how to use the machine properly, as incorrect use can lead to serious injury.
An ultrasonic welder can be used to create high-quality, reliable products in a wide range of industries. The technology is a cost-effective and environmentally friendly alternative to other manufacturing techniques, making it ideal for companies seeking to streamline their production processes. However, it is important to understand the technology and its capabilities before purchasing an ultrasonic welder for your business. For optimal results, choose a welder with patented Melt-Match technology, which synchronizes the motion of the weld horn with the melting point of your plastic material.